Nuclear fusion is a promising source of massive and clean energy for humanity. The fusion fuels are abundantly available on the planet and the by-products of fusion reaction have low burden of waste for the future generations. ITER is an international project and is part of a series of experimental fusion reactors which are meant to investigate and demonstrate the feasibility of using nuclear fusion as a practical source of energy. During the Deuterium-Tritium fusion reactions, plasma facing components of the vacuum vessel will be damaged from the particle bombardment. These components will require several replacements during the lifecycle of the reactor. The presence of beta and gamma activated components within the vessel, together with hazardous dust, preclude the possibility of any human access. The maintenance operations of the reactor require the use of remotely operated robots.
3D model of ITER fusion reactor with a cross section of vacuum vessel (Image credit: VTT Technical Research Centre of Finland)
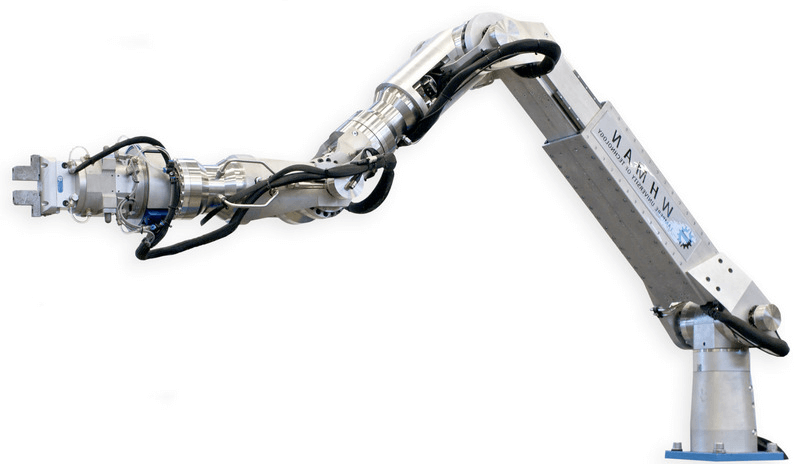
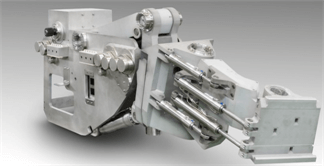
After international competition the VTT Technical Research Centre of Finland together with Tampere University of Technology was chosen to host the Divertor Test Platform (DTP2) research facility. DTP2 is a full scale model of the divertor region of the ITER fusion reactor. Through extensive research, several water hydraulic robots have been designed, developed and tested at this facility. Larger robots can carry components as heavy as 10 tons in and out of the reactor following predefined position trajectories with an accuracy of 2–3 millimetres (left in the picture above). Smaller robots with a load capacity of 100 kg can function in full master-slave mode during teleoperation (right in the picture above). These unique developments in the field of robotics have ensured the use of nuclear fusion as a possible source of energy in future.
Video: “Divertor Test Platform (DTP2)” on YouTube
Acknowledgments and Contact:
Dr. Ali Muhammad
VTT Technical Research Centre of Finland
Systems Engineering
Tekniikankatu 1, PL 1300
33101 Tampere
Finland
Phone: +358 20 722 4077
Fax: +358 20 722 3499
ali.muhammad@vtt.fi
www.vtt.fi