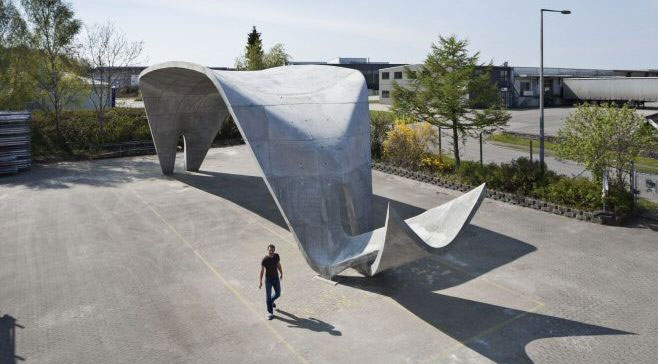
The six meters high and 21.4 meters long concrete fish appearing in front of Paschal – Danish administration building in Aarhus in Denmark, has been cast in such advanced molds made with robots (Image credit: Danish Technological Institute)
A large concrete sculpture representing a fish marks the end of the 4-year EU project ‘TailorCrete’. The concrete sculpture was created by digital 3D modeling, which also formed the basis for the production where robots have been the key to translate the digital models into physical creation.
Most often you associate concrete casting with square blocks used for ugly or boring constructions. The project ‘TailorCrete’ changes that. The goal has been to develop new industrial methods for the production of future concrete casting molds in exciting shapes. Making molds for concrete in unconventional shapes in the usual manner is a costly affair. But when robots cut molds from polystyrene (EPS) it can be done much cheaper. And the polystyrene can be used again!
Robot creates mold from polystyrene
The special reinforcement, which is the sculpture skeleton, is also bent by robots. The sculpture is the culmination of a project launched by the Danish Technological Institute back in 2007.
- The overall objective has been to create beautiful buildings with exiting shapes. For instance with double curved surfaces in concrete, says Kurt Nielsen from the Center for Robotics at the Danish Technological Institute.
- To reach the objective, there have been some different challenges to be solved: First, to develop a concrete that without vibration can flow out even in very special shapes, secondly to construct complex molds using robots, and third to automate the production of the required reinforcement, which keep the structure in place. Especially the latter has been a major challenge.
For special geometries, the production of the required reinforcement is often difficult because of the need to follow the geometry within strict tolerances. The project has developed a manufacturing process in which two robots work together to produce the complex mesh. Based on the digital models one robot bows thus the reinforcing bars, while the other robot is responsible for bonding reinforcement in a network. The method is used the most complicated sites related about the design of the sculpture.
An example of a robot cutting molds from polystyrene (EPS) (Image credit: Danish Technological Institute)
Reusable molds in complex molds milled of robots
In order to cast the complicated form, has been developed a special type of concrete – a self-compacting concrete – as well as a related form filling strategy. This combination ensures concrete surfaces of high quality that can last for many years.
The frame, which encloses the concrete, and is thus outside the body, is specially developed for the project. Thus formed shuttering parts of blocks of expanded polystyrene (EPS ), which is milled through robotics at the Technological Institute, and then covered with a special silicone membrane. The membrane ensures smooth surfaces, good release properties and above all possibility of reuse of the mold parts, as demonstrated through concrete fish, where 80 % of all form parts recycled. After moldings may EPS portion further granulated and recycled into new EPS production.
Check the robots in manufacturing gallery for further images.
Acknowledgments and Contact:Kurt Nielsen
Danish Technological Institute
Robot Technology
Forskerparken 10F
5230 Odense
Denmark
Phone: +45 72 20 20 00
kuni@teknologisk.dk
www.teknologisk.dk